Share
Pin
Tweet
Send
Share
Send
Is it possible to make a printed circuit board of acceptable quality at home without a printer? Yes. Can. Moreover, if everything is done as described in the material, it will take quite a bit of money and time, and the quality will be at a very high level. In any case, the electric current "runs" along such paths with great pleasure.
The list of necessary tools and consumables
It’s worth starting with the preparation of tools, fixtures and supplies, which you simply can’t do without. To implement the most budgetary method of manufacturing printed circuit boards at home, you will need the following:
- Drawing design software.
- Transparent plastic wrap.
- Narrow tape.
- Marker.
- Foiled fiberglass.
- Sandpaper.
- Alcohol.
- Waste Toothbrush.
- Tool for drilling holes with a diameter of 0.7 to 1.2 mm.
- Ferric chloride.
- Plastic container for etching.
- Paint brush.
- Soldering iron.
- Solder.
- Liquid flux.
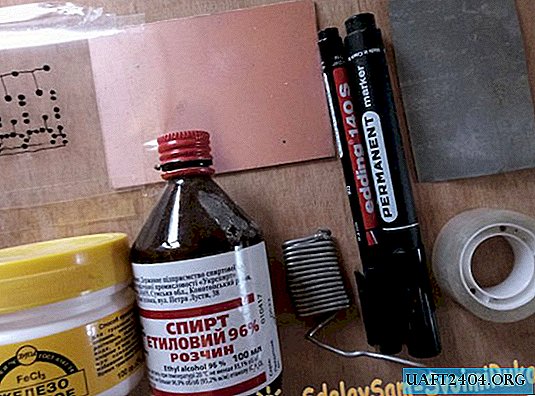
We will go through briefly on each item, as there are some nuances that can only be reached by experience.
There are a huge number of programs for developing printed circuit boards today, but for a beginner amateur, the Sprint Layout is the easiest option. It’s easy to learn the interface, you can use it for free, there is a huge library that includes common radio components.
Polyethylene is needed to transfer the picture from the monitor. Better to take the film harder, for example, from old covers for school books. Any tape is suitable for attaching it to the monitor. It is better to take a narrow one - it will be easier to peel off (this procedure does not harm the monitor).
The markers should be discussed in more detail, since this is a sore subject. To transfer the pattern to polyethylene, in principle, any option is suitable. But for drawing on foil-coated fiberglass, a special marker is needed. But there is a little trick here, how to save money and not to buy expensive “special” markers for drawing printed circuit boards. The fact is that these products by their properties are absolutely no different from ordinary permanent markers, which are sold 5-6 times cheaper in any stationery store. But the marker must necessarily have the inscription "Permanent". Otherwise, nothing will work.

Foiled fiberglass can be taken any. Better if it is thicker. Beginners with such material are much easier to work with. To clean it, you will need sandpaper with a grain size of about 1000 units, as well as alcohol (there is in any pharmacy). The last consumable can be replaced with a liquid for mixing nail polish, which is in any house where a woman lives. However, this remedy smells rather nasty and weathered for a long time.
To drill the board, it is better to have a special mini-drill or engraver. However, you can go a cheaper way. It is enough to buy a collet or cam chuck for small drills and adapt it to a conventional household drill.
Ferric chloride can be replaced with other chemicals, including those that are probably already in your home. For example, a solution of citric acid in hydrogen peroxide is suitable. Information on how alternative compositions for etching boards are prepared for etching boards can be found on the Web without any problems. The only thing worth paying attention to is the container for such chemistry - it should be plastic, acrylic, glass, but not metal at all.
About soldering iron, solder and liquid flux, it’s not worthwhile to speak in more detail. If the radio amateur came to the issue of manufacturing a printed circuit board, then he is probably familiar with these things.
Development and transfer of a board drawing to a template
When all of the above tools, fixtures and consumables are prepared, you can take on the development of the board. If the device being manufactured is not unique, then it will be much easier to download its project from the Web. Even a regular JPEG image will do.

If you want to go in a more complicated way - draw a board yourself. This option is often unavoidable, for example, in situations where you do not have exactly the same radio components that are needed to assemble the original board. Accordingly, replacing the components with analogues, under them you have to allocate space on the fiberglass, adjust the holes and tracks. If the project is unique, then the board will have to be developed from scratch. For this, the aforementioned software is also needed.
When the board layout is ready, it remains only to transfer it to a transparent template. Polyethylene is fixed directly on the monitor using tape. Next, we simply translate the existing drawing - tracks, contact spots and so on. For these purposes, it is best to use the same permanent marker. It is not erased, not smeared, and it is clearly visible.
Preparation of foil fiberglass
The next step is the preparation of fiberglass. First you need to cut it off by the size of the future board. It is better to do this with a small margin. For cutting foil fiberglass, you can use one of several methods.
Firstly, the material is perfectly cut with a hacksaw. Secondly, if you have an engraver with cutting wheels, it will be convenient to use it. Thirdly, fiberglass can be cut to size with a clerical knife. The principle of cutting is the same as when working with a glass cutter - a cut line is applied in several passes, then the material is simply broken off.


Now, it is necessary to clean the copper layer of fiberglass from the protective coating and oxide. There is no better way than sandpaper to solve this problem. Granularity is taken from 1000 to 1500 units. The goal is to get a clean, shiny surface. It is not worth stripping the copper layer to a mirror shine, as small scratches from sandpaper increase the adhesion of the surface, which will be needed next.
In conclusion, it remains only to clean the foil from dust and fingerprints. To do this, use alcohol or acetone (nail polish remover). After processing, we do not touch the copper surface with our hands. For subsequent manipulations, we capture fiberglass beyond the edges.
The combination of the template and fiberglass

Now our task is to combine the pattern obtained on polyethylene with prepared fiberglass. For this, the film is superimposed on the right place and positioned. The remnants are wrapped on the back side and fastened using the same adhesive tape.


Drilling holes
Before drilling, it is recommended that you somehow fix fiberglass with a template on the surface. This will allow for greater accuracy, and also eliminate the sudden turning of the material during the passage of the drill through. If you have a drilling machine for such work, then the described problem will not arise at all.

You can drill holes in fiberglass at any speed. Someone works at low speeds, someone at high speeds. Experience has shown that the drills themselves last much longer if they are operated at low speeds. So they are more difficult to break, bend and damage the sharpening.
Holes are drilled directly through polyethylene. The reference points will be the future contact spots drawn on the template. If the project requires it, then timely change the drill for the desired diameter.
Drawing tracks
Next, the template is removed, but not discarded. We still try not to touch the copper coating with our hands. To draw tracks we use a marker, always permanent. It is clearly visible on the trail that he leaves. It is better to draw in one pass, since after hardening the varnish, which is part of a permanent marker, it will be very difficult to make corrections.

As a guide, we use the same polyethylene template. You can also draw in front of the computer, referring to the original layout, where there are markings and other notes. If possible, it is better to use several markers with tips of different thicknesses. This will allow for better rendering of thin tracks and extensive polygons.


After drawing the drawing, we definitely wait for some time necessary for the final hardening of the varnish. You can even blow dry. The quality of future tracks will depend on this.

Etching and cleaning tracks from the marker
Now the fun part is etching the board. There are several nuances here that few people mention, but they significantly affect the quality of the result. First of all, we prepare a solution of ferric chloride according to the recommendations on the package. Usually the powder is diluted with water in a ratio of 1: 3. And here is the first tip. Make the solution more saturated. This will help speed up the process, and the drawn tracks will not fall off before everything you need is wiped out.

Immediately the second advice. It is recommended to immerse the bath with the solution in hot water. You can heat it in a metal bowl. An increase in temperature, as is known since the school curriculum, significantly accelerates the chemical reaction, which is the etching of our board. Reducing the time of the procedure is at hand. Marker paths caused by the marker are quite unstable, and the less they get acidic in the liquid, the better. If at room temperature the charge in the ferric chloride is etched for about an hour, then in warm water this process is reduced to 10 minutes.
In conclusion, another tip. In the process of etching, although it is already accelerated by heating, it is recommended to constantly move the board, as well as to clean off the reaction products with a brush for drawing. Combining all the above manipulations, it is quite possible to corrode excess copper in just 5-7 minutes, which is simply an excellent result for this technology.

At the end of the procedure, the board must be thoroughly washed under running water. Then we dry it. It remains only to wash off the traces of the marker, still covering our paths and spots. This is done all the same with alcohol or acetone.

PCB Tinning
Before tinning, we must again walk through the copper layer with sandpaper. But now we are doing this very carefully so as not to damage the tracks. The easiest and most affordable way to tin is traditional, using a soldering iron, flux and solder. You can also use alloys of Rose or Wood. There is also the so-called liquid tin on the market, which can greatly simplify the task.
But all these new technologies require additional costs and some experience, therefore, for the first time, the classical tinning method is also suitable. Liquid flux is applied to cleaned tracks. Next, solder is collected on the soldering iron tip and distributed over the copper remaining after etching. It is important to warm the tracks, otherwise the solder may not “stick”.

If you still have Rose or Wood alloys, then you can use them not by technology. They simply remarkably melt with a soldering iron, are easily distributed along the tracks, do not stray into lumps, which will be only a plus for a beginner radio amateur.
Conclusion
As can be seen from the above, the low-cost technology for the manufacture of printed circuit boards at home is really affordable and inexpensive. Neither a printer, nor an iron, nor an expensive photoresistive film is needed. Using all the tips above, you can easily make the simplest electronic crafts without investing a lot of money in it, which is very important in the early stages of amateur radio.

Share
Pin
Tweet
Send
Share
Send